
When it’s up and running properly, your cooling tower is the quiet workhorse and unsung hero of your water system. But neglecting regular inspections, cleaning, and maintenance can lead to hundreds of thousands of dollars down the drain. Here’s how to keep it running at optimum levels of efficiency and performance – both for cost savings and for the environment.
Limited Margin of Error
The cooling tower has one job: to reduce water temperature.
It does this by bringing air and water together inside the tower, allowing some water to be evaporated, which then reduces the temperature of the water being circulated through the tower.
Simple right?
Darius Barkauskas, Technical Director at HOH, says there’s a limited margin of error when it comes to operating cooling towers:
“It’s a lot easier to damage a cooling tower than a boiler. During a hot summer like we’re seeing right now, improper control for a few days can lead to serious heat transfer reduction and serious damage.”
Some industries, like food processing, face high stakes as they rely heavily upon their cooling towers for regular operations.
“Our customers in the food processing facilities require continuous refrigeration to keep meat from spoiling – if their condensers malfunction they’ll lose millions,” Barkauskas explains.
All facilities, regardless of their industry or function, need to closely monitor their cooling tower operations before a problem arises.
“When your cooling tower is not operating efficiency it will cost you money due to increased energy consumption. It can also put you at risk for being outside of compliance with energy standards for your industry,” says Barkauskas.
Mistakes That Hurt the Performance of Your Cooling Tower
At HOH we help facility managers avoid mistakes that could be wasting money and hurting their equipment. Here are four of the most common things we see:
1. Turning a Blind Eye
Not having eyes on your cooling tower and not conducting cleanings with the appropriate chemical treatments.
“We’ve seen normal debris like leaves, but we’ve also seen birds caught in cooling towers and even concrete dust from construction sites a mile away. If you’re not looking at your cooling tower regularly, a problem can sneak up on you,” advises Barkauskas.
Service Fact: HOH can apply chemicals to clean your cooling towers both continuously and/or for remediation purposes.
2. Biofilm Growth
Never forget to monitor and control biofilm growth.
“Once biofilm attaches to the surfaces, slime will grow and spread and reduce your heat transfer efficiency. It can also promote scaling – which causes major damage to your system, including possible corrosion.”
3. Out-of-Date Control Systems
If you haven’t upgraded to smart controls yet, it’s time. The initial investment pays for itself many times over in the energy, manpower, and maintenance dollars you save over the life of your cooling tower.
4. Wrong-Sizing Your System
It’s critical to have the right-sized system for your facility’s usage.
A system that is too large will have high residence times and lead to scaling without proper system turnover or feeding acid products.
Conversely, a system that is too small for your operation can lead to system shutdowns because it runs out of water.
According to Barkauskas, “We have these two identical buildings in Chicago for one client. But their volume/usage are vastly different so we treat them with two different methodologies.”
Improving Cooling Tower Performance
Here are the best practices for keeping your cooling tower performing at optimum levels:
Better Monitoring
Install flow meters on make-up and bleed-off lines to verify how much water is actually being used. Then upgrade your control system with a smart system to remotely monitor from anywhere.
Pathogen Control
Have a regular onsite analysis of your water performed by a water treatment partner (as well as a remediation plan if anything is found) to make sure that your building gets a clean bill of health.
“The majority of Legionella outbreaks start in the cooling tower,” says Barkauskas.
Regular Inspections
Do weekly or even daily inspections for debris or leaks to ensure that there’s nothing clogging your tower and that no fouling or scaling has occurred.
Cleaning
Conduct semi-annual cleaning for systems that run summer-only and quarterly for systems that run all year.
Proper Winterization
Prepare for low-load or shut down for the longevity of your equipment and to prevent pathogen growth over the winter.
Pro Tip: Look for Evaporation Credits!
Many cities will provide you with evaporation credits from your cooling tower to offset some of your costs, but you have to be able to show data. This is another reason why it’s critical to have an up-to-date monitoring system.
Get Help From A Water Treatment Partner
Barkauskas says that poor-functioning cooling towers can be a silent drain on your budget.
“Customers often come to us with a problem with the cooling tower itself not realizing that it’s impacting their operational costs. Lack of good control and not having a good program means you’re flushing money down the drain.”
HOH specializes in cooling water programs and can help you prevent pathogen growth to lower your risk and reduce your energy and utility costs to save you money.
Our mission at HOH is to ‘Make a lasting impact with water’ so we also want to stress the environmental cost of inefficiency.
Barkauskas agrees: “There is a finite amount of fresh water on the planet. If you’re not looking for ways to be more efficient right now, you’re putting us all behind the curve.”
Recent Blog Posts
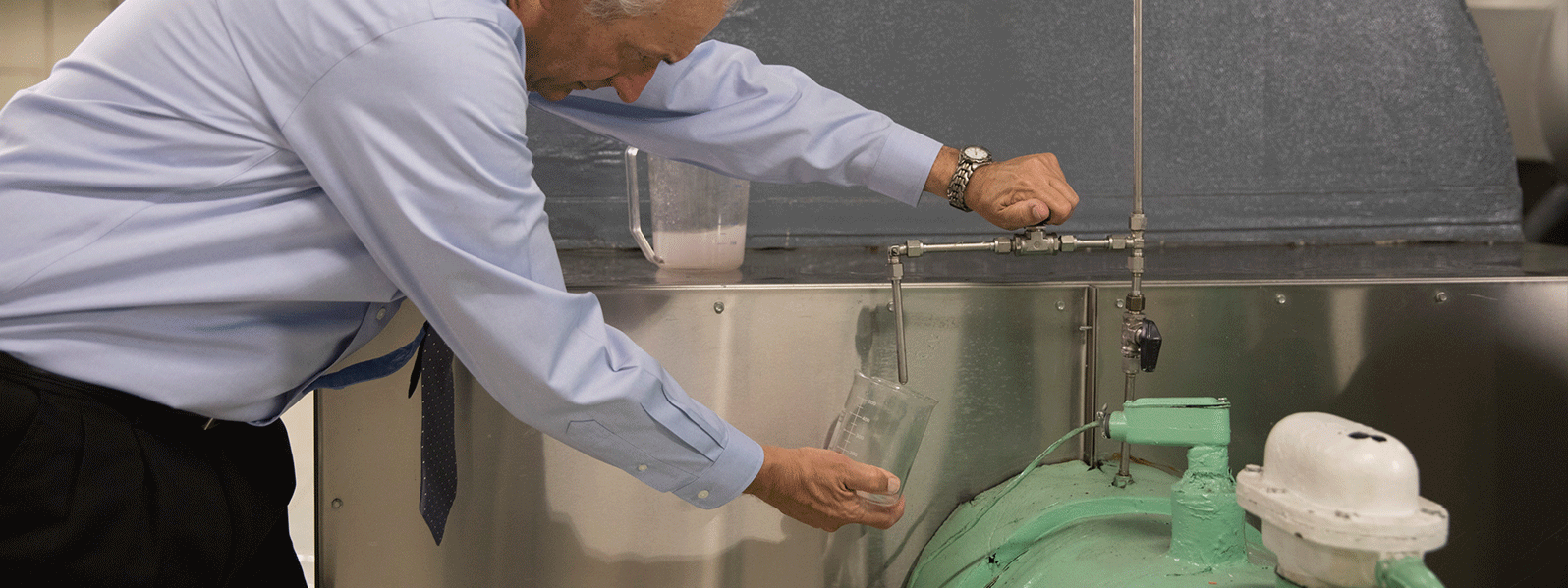
Five Ways to Increase the Efficiency of Your Closed Loop System

Global 6K for Water
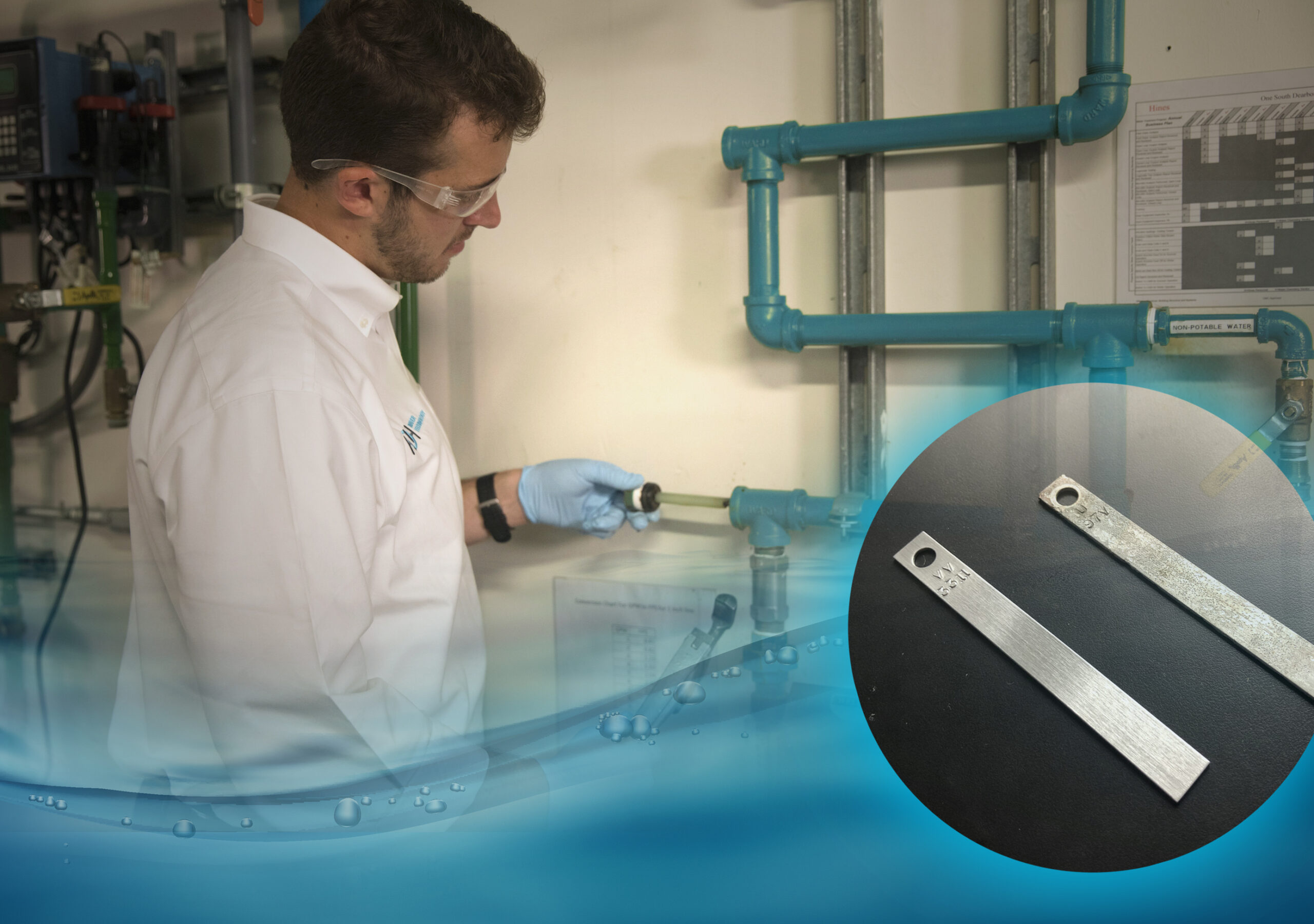